Chem-Trend® Sealers and Preparation Pastes provide a durable barrier to prevent mechanical and chemical bonding during molding operations. These products are an excellent way to prepare new tooling and to provide an effective base for enhancing release from difficult mold surfaces. Our mold sealers and pastes have been formulated to work most efficiently in combination with Chem-Trend® release agents in pre-production or on-line production touch-up applications.
Polyurethane
Release Agents and Mold Cleaners for the Polyurethane Industry
Our history in the polyurethane industry started nearly 60 years ago, when our founder was a significant contributor to the evolution of polyurethane seat cushion production for the automotive industry. Since that time, we have been leading innovation, thanks to our vast worldwide research and development resources, dedicated to creating solutions to customer challenges as well as paving the way for the future.
With a focus on increasing the quality of your products, we work to maximize productivity, efficiency, and safety, while reducing waste and error. In addition, we are committed to sustainability in both improving our footprint (our direct impact) as well as our handprint (the impact we can create for our customers). We are far more than a creator of products; we add value to each of our customers each and every day.
Our Chem-Trend® portfolio of products helps to provide comprehensive solutions to the polyurethane industry.
Related
High Pressure Injection Molding for Polyurethane Moulding
The capability to simulate real production conditions of polyurethane molding is critical in engineering industry-leading release agents. Evaluating and improving our mold release agents helps our customers perform at their highest efficiency, quality, and sustainability. Watch the video to see the high pressure injection molding system in action.
Application of Chem-Trend® mould cleaners in polyurethane moulding processes
Tutorial number 1 – polyurethane application: The video demonstrates how to properly clean a mould with the help of some tools and a highly efficienct Chem-Trend Mould Cleaner.
Application of Chem-Trend® mould sealers and paste waxes in polyurethane moulding processes
Tutorial number 2 – polyurethane application: The video demonstrates the different methods to prepare the mould before startup of production by use of paste wax or sealer.
Spray equipment and testing in polyurethane moulding processes
Tutorial number 3 – polyurethane application: The video explains what kind of spray equipment is available for mould release agent application of polyurethane foam manufacturing. It demonstrates what should be considered when adjusting and using the spray equipment to assure best application practices.
Improper spray application of release agents in polyurethane moulding processes
Tutorial number 4 – polyurethane application: The video demonstrates what mistakes can be done when applying a release agent to a mould prior to the startup of a polyurethane moulding process.
Release Agents
Our mold release agents for polyurethane provide a competitive advantage to the largest and smallest manufacturers alike. We offer water and solvent-based release agent solutions along with carrier-free solutions that can maximize productivity while meeting the most demanding specifications and operating conditions. We work with manufacturers on applications that include:
- Integral skin
- PU spray skin
- Shoe sole manufacturing
- High-resiliency foam for seating, acoustical, and carpet
- Insulation back foaming
- Visco-elastic polyurethane products
- Rigid foams
- Dual-density and single-density shoe soles
- Isocyanate-bound products
- Cast elastomers
- Microcellular urethane applications such as jounce bumpers
Related
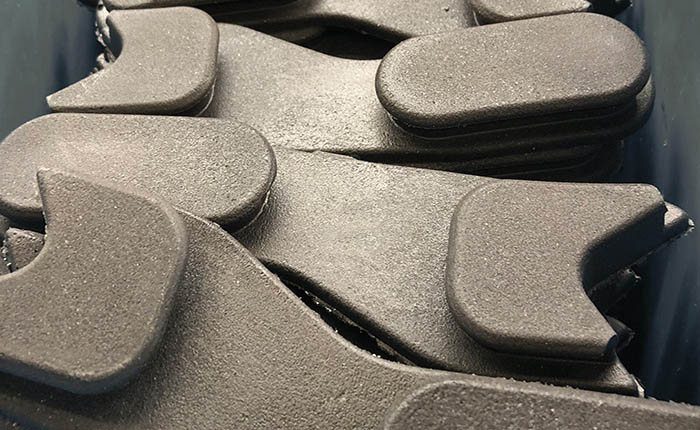
Water-based release agent allows for time-saving improvements in polyurethane back foam application.
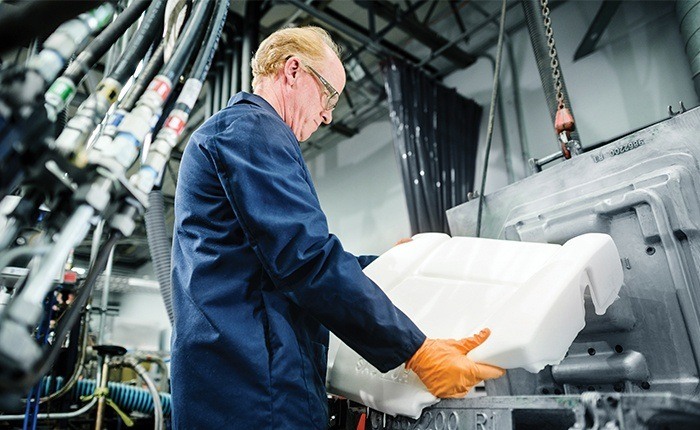
A more efficient release agent is changing the production of two-wheeler seats made of PU foam.
Sure-Footed at all Molding Steps
Chem-Trend provides customized technologies to effectively optimize productivity for your shoe sole manufacturing processes.
Achieving Better Bottom-Line Benefits with Chem-Trend’s Integral Skin Moulding Aids
Chem-Trend offers process aids that aim to assist in the integral skin moulding process. These aids are designed to provide several potential benefits for processors:
Surface Appearance: Chem-Trend’s aids can help achieve a consistent surface quality, which is critical for the aesthetic aspect of the final product.
Adhesion: The aids may improve the bonding between different materials, which is important for the structural integrity of the moulded items.
Release: They can facilitate the demoulding process, potentially reducing the time each cycle takes and possibly leading to more efficient production schedules.
Defects: Using these aids might lead to a decrease in the number of defects, which can be beneficial for maintaining production standards.
Buildup: The aids are formulated to minimize residue accumulation in the mould, which could reduce the frequency of maintenance stops.
In summary, Chem-Trend’s process aids are formulated to support the integral skin moulding process, with the intention of improving product quality and process efficiency.
Ancillary Products
Mold Cleaners for Polyurethane Molding
Chem-Trend® Mold Cleaners are designed to address the needs of virtually any type of polyurethane manufacturing process. They are formulated to powerfully but safely attack resinous mould build-up. These highly engineered cleaners are designed to remove waxes, silicones, contaminants, polyurethane and polyurea residues from both pre-production mold preparation and on-line molding applications. Mold cleaners can be supplied as a liquid or a gel, depending on your process. In fact, by using our mold cleaners, some customers have eliminated the need for expensive dry ice blasting.
Mold Sealers and Preparation Pastes for Polyurethane Molding
Low-Pressure Mixing Head Flush Solutions for Polyurethane Molding
Chem-Trend® Head Flush Solutions can be used to effectively clean out the mixing head chamber in certain low pressure processing applications. Our head flush solutions are easy-to-handle and are the most powerful resin removers available for polyurethane systems. Long down time to allow for cleaning between successive shots can be eliminated with these highly efficient, fast drying solvents. For customers using different coloured polyurethane systems through the same mix head, our head flushing products can help minimize scrap between colour changes.
Anti-Squeak/Noise Reduction Products for Polyurethane Molding
Our anti-squeak products are water-based. They’re applied to eliminate squeak wherever rubbing could cause noises that might be heard by the end user.
Contact Us
SprayIQ™ and DilutionIQ™ support Industry 4.0 IOT digitalization efforts in spray application of release agents.
SprayIQ™ device measures the amount of release agent applied per spray cycle and time per spray cycle.
Chem-Trend’s DilutionIQ™ System Keeps Customers Connected with Remote Monitoring.
Related
SprayIQ™
SprayIQ™ technology measures the amount of release agent applied per spray cycle. As soon as the spraying begins, you’ll know your volume and when your threshold has been reached.
DilutionIQ™
Customers using concentrated release agents have always looked to maintain an exact proportion of concentrate and water. That is why DilutionIQ™ was created for customers purchasing Chem-Trend release agent concentrates to allow for remote monitoring of the process, ensuring optimal dilution rates are maintained.
How to recognize, understand and solve problems with polyurethane moulding
Polyurethane (PU) moulding is a versatile process used in various industries, from automotive to footwear. However, like any manufacturing method, it comes with its share of challenges. We offer a concise overview of common PU moulding problems and their solutions.
Get an overview about common problems in different application areas and how to solve those.
To learn more about how we have developed advanced products to address the specific challenges found in polyurethane manufacturing, contact us today.
FAQ
There are some concrete release agents that are low or zero VOC. This needs to be investigated when discussing the characteristics and attributes of different release agents with potential suppliers.
This is an area of growing concern and interest and there are products available that have low and zero VOC materials.
Chem-Trends High Performance Release Agents are usually VOC free or VOC reduced. Before using these products, the legal requirements on site and the application parameters must be determined (e.g. 5 tonnes VOC or TA-Luft 50mg/m³).
Depending on the production set up a wide variety of configurations can be utilized. From manual HVLP guns to automated spray systems, assistance with determining the best selection to efficiently apply concrete release agents should be provided by the release agent supplier.
Watch our video tutorials for more information.
Materials may be diluted through very reliable wall mounted or floor model proportioners. These units provide a consistent water to concentrate ration that allows for a dependable mix without the use of valuable manpower.
By using a piece of cardboard a spray pattern may be tested. First make sure the spray equipment nozzle and air cap are clean and unrestricted. Hold the spray gun a distance from the cardboard that is a normal distance from the spray gun to the moulding surface. Spray the mould release onto the cardboard in a sideways sweeping motion. The pattern should be solid yet dry quickly. Any splotches will show areas that may be under sprayed or unevenly applied. Liquid running down the surface means the liquid is being applied too heavily.
Please see our tutorial application video how to correctly apply a mould release agent in polyurethane moulding applications.
When applying a release agent with manual spray it is important to establish a baseline throughput to maintain a consistent spray. Required throughput amounts will vary based on the tooling grain, part complexity, and the speed of the line. When a proper spray amount is determined the throughput in grams or milliliters per second should be recorded. This should be checked each shift to make sure there is consistency between operators. This information will help to train new operators to correctly apply the release agent. Consistent fluid and atomizing air pressures are also a must for repeatable application.
The key is to have a dry mould surface before the foam is poured. A liquid carrier is used to deliver the release agent to all surfaces of the tooling. This carrier should be evaporated before the foam is poured or injected into the tool.
Key selection factors are:
- Type of foam being produced (rigid, seating, RIM, etc.)
- Moulding temperature range
- Mould material (aluminum, steel, etc.)
- Time between mould release application and foam pour
- Cure time
- Foam density
- Post moulding requirements (bonding, painting, etc.)
The more information on the process the easier it is to determine the perfect release agent.
Obviously enabling the easy removal of cured parts from different moulded materials is an important reason for using a release agent. What many do not consider is that these same materials can greatly increase mould life by maintaining a lubricious film on the mould surface that will prevent the cured concrete from deteriorating the interface. These products can also aid in the wetting out of pigments and improve colour transfer from the mould substrate to the stone. This can help to minimize scrap caused by colour changes. All of these benefits result in a more efficient operation.
Hybrid products provide the benefits of a solvent based material, such as an open surface and faster film formation and evaporation, but they utilize a waterborne carrier with a small amount of solvent to provide these benefits. This technology significantly minimizes VOC emissions.
Various release agents can be used with many forms of spray equipment. While HVLP systems are the most common method of application, many other methods can be used based on equipment and plant configurations.
Please see our tutorial application video about that topic.
Release agents for veneer/masonry stone applications and other specific concrete applications should be designed to allow pigments to wet out on the surface and to keep moulds clean through improved colour transfer. Maintaining a proper application amount and/or dilution is important in achieving these goals and the effectiveness of the release agent should be fully evaluated in a field trial prior to full scale adoption.
By using a piece of cardboard a spray pattern may be tested. First make sure the spray equipment nozzle and air cap are clean and unrestricted. Hold the spray gun a distance from the cardboard that is a normal distance from the spray gun to the moulding surface. Spray the mould release onto the cardboard in a sideways sweeping motion. The pattern should be solid yet dry quickly. Any splotches will show areas that may be undersprayed or unevenly applied. Liquid running down the surface means the liquid is being applied too heavily.
Watch our polyurethane application tutorial video about how to test the spray equipment.
When applying a release agent with manual spray it is important to establish a baseline throughput to maintain a consistent spray. Required throughput amounts will vary based on the tooling grain, part complexity, and the speed of the line. When a proper spray amount is determined the throughput in grams or milliliters per second should be recorded. This should be checked each shift to make sure there is consistency between operators. This information will help to train new operators to correctly apply the release agent. Consistent fluid and atomizing air pressures are also a must for repeatable application.
For manual application, it is important to determine the appropriate parameters via nozzle size, release agent quantity and atomising air. In order to obtain a clean spray pattern according to the specifications of the moulded part, the release agent quantity must first be determined via nozzle and material pressure. Then the atomising air must be adjusted so that the mould can be wetted evenly and quickly.
Paste waxes provide an excellent barrier for starting up on clean moulds. These materials provide protection in scratched, cold, or high pressure areas, and provide a durable layer that will help to minimize complications due to defects on the metal surface. Mould sealers improve the performance of the release agent by creating an optimal surface to release the parts from. Sealers are applied only to freshly cleaned tools but the benefit lasts throughout the production and cleaning cycle.
Please watch our polyurethane tutorial video about how to clean and seal a mould.