Wood Composites: faster, safer, better
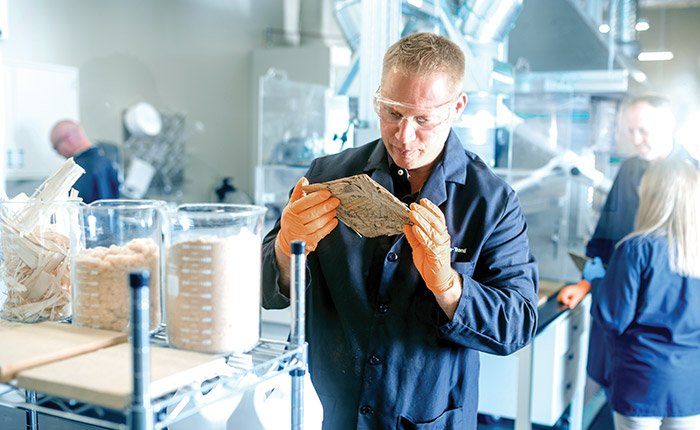
Case Study Wood Composite:
Where there’s smoke, there’s opportunity for improvement.
WHAT WE ACHIEVED.
A global leader in composite wood manufacturing was experiencing a myriad of performance issues. Through a committed and comprehensive process, Chem-Trend’s team was able to effect improvements, eliminating smoke and overspray common to the manufacturer’s procedure and achieving excellent performance on all board thicknesses and temperature profiles. We advanced their capability to increase application rate without press belt buildup.
We helped boost line speed by 5-7% with heavier application rates while demonstrating a 2% reduction in changeover downtime. This led to record production months.
HOW WE GOT THERE.
The wood composites manufacturer was seeking a more consistent approach that solved both their underspray and overspray issues. Light spray risked sticking of large sections of board, which required operators to work near hot press belts to manually scrape it off. Heavy spray helped prevent sticking and could possibly gain some line speed. While overspray was the preferred method, it resulted in buildup, overspent filters, and smoke. Fusing the manufacturer’s operational expertise and product knowledge with Chem-Trend’s process-enhancing chemical specialty formulas, together we were able to eliminate these impeding factors from the line.
OUR SOLUTION.
We engaged with our research and development team, collaborated with the client through multiple trials, and provided training to operators. This dedication resulted in a no-smoke solution and an elimination of issues related to overspray while simultaneously realizing higher productivity overall.
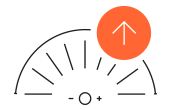
DATA INSIGHTS
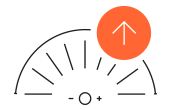
HANDPRINT IMPACT
At Chem-Trend, we pride ourselves on our long history of sustainability efforts. However, it is our effect on our customers’ processes that provides the greatest impact. It goes beyond our global Footprint; it is our even wider Handprint.
Here, we achieved the following:
At Chem-Trend, we pride ourselves on our long history of sustainability efforts. However, it is our effect on our customers’ processes that provides the greatest impact. It goes beyond our global Footprint; it is our even wider Handprint.
Here, we achieved the following:
- Less product waste due to a reduction of overspray
- Less energy waste via a reduction in equipment downtime
- Cleaner, safer work environment
Materials
Waste
Health