Semi-permanent release agent boosts productivity for a manufacturer of pre-cured tyre treads.
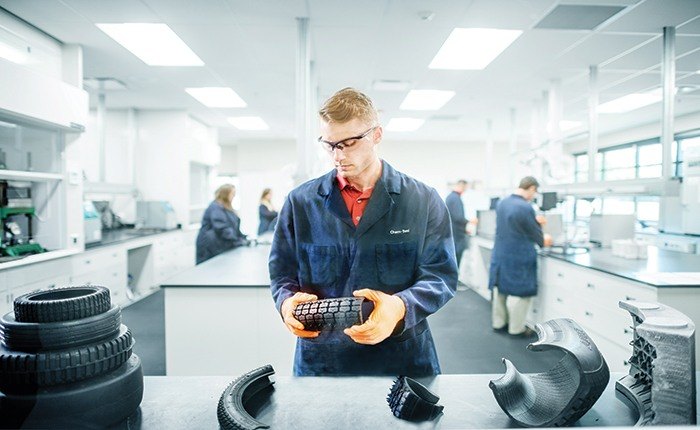
Case Study Tyre:
A high-quality tire thanks to a new release agent.
WHAT WE ACHIEVED.
A high percentage of moulding defects leads to tremendous waste and opportunity cost for producers of pre-cured tread strips. A large manufacturer in the tyre tread business was noticing a high percentage of moulding defects when using a diluted silicone emulsion as a release agent on pre-cured treads. Using one of our high-performing semi-permanent mould coatings, we helped the customer to reduce their moulding defects by 75% while cutting their release agent consumption nearly in half. In addition to this, the customer saw cleaner treads, which positively influenced finished tread appearance and downstream processing.
HOW WE GOT THERE.
Through a multistage process, we worked with the manufacturer to analyze the situation and identify several potential solutions. We were able to optimize the spray application system, and we subsequently trained the operators on the optimal application techniques to ensure maximum effectiveness.
OUR SOLUTION.
Unlike the diluted silicone emulsion the manufacturer was previously using, the solution we offered was ready to use and did not require any dilution or other preparation. It needed applying only a few times per day compared to their previous process, which required attention during each curing cycle. The moulds stayed cleaner and remained in service for longer periods between cleaning cycles. There was minimal-to-no transfer of the mould coating to the tread surface, which greatly reduced the time needed in downstream processes to prepare the underside of the pre-cured tread.
With one change, Chem-Trend positively affected nearly every step of the process, reducing the amount of release agent used by 45% while saving time, cutting down on defects, and creating a superior finished product.
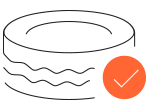
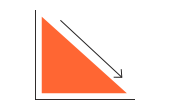
DATA INSIGHTS
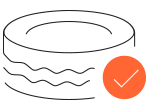
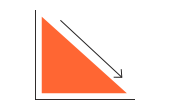
HANDPRINT IMPACT
At Chem-Trend, we pride ourselves on our long history of sustainability efforts. However, it is our effect on our customers’ processes that provides the greatest impact. It goes beyond our global Footprint; it is our even wider Handprint.
Here, we achieved the following:
- Less raw material wasted due to reduction in moulding defects
- Less release agent required reduces transportation and packaging needs, positively impacting the environment
- Cleaning frequency and use of associated products reduced
Materials
Waste